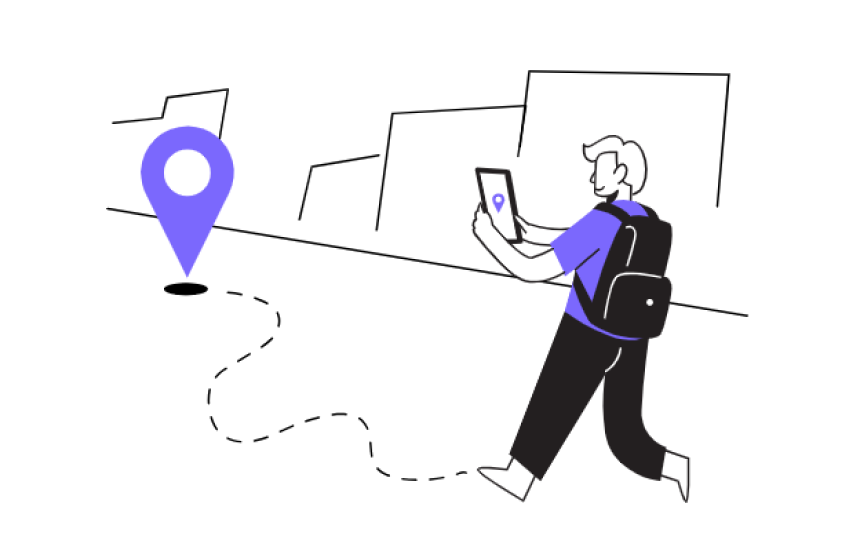
Globally, solar energy production is expanding everywhere. The Inflation Reduction Act of 2022’s renewable energy provisions has sparked well over $100 billion in private sector investment in the US, with 51 new solar manufacturers announced or expanded.
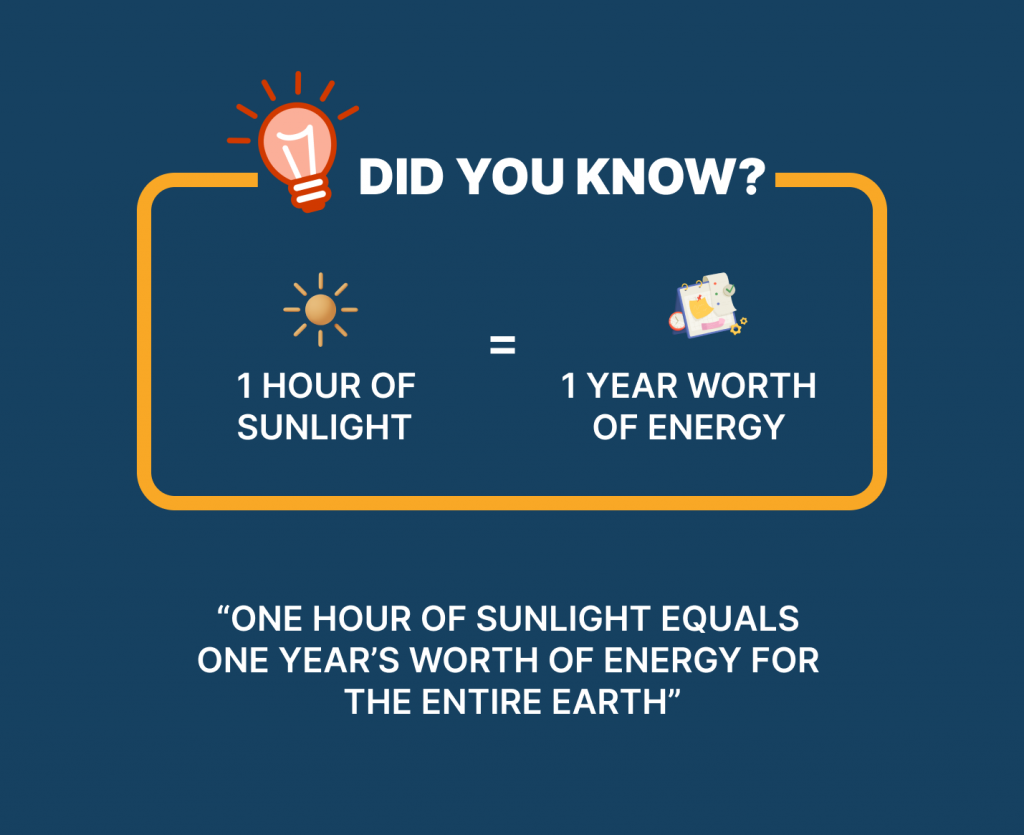
The United States is predicted to have installed 669 GW of solar capacity by 2033, which is more than four times as much as was built in 2023. Now, let us briefly discuss the importance of solar inspection, its steps and how field tracking software provides timely solar inspection in your industry.
How to prepare for your solar inspection?
Table of Contents
- Determine the AHJ of your installation before planning the design and obtaining the necessary permits. Verify that your plans comply with all applicable building, electrical, fire, residential, wind, and utility interconnection codes.
- For installation of the system and any associated work, submit your designs to the AHJ and obtain permission.
- Obtain a separate connecting permit from the property’s electric utility. (Before submitting an interconnection application, certain utilities need an AHJ-approved permit.)
- Arrange the installation with the homeowner after the permits are authorized.
- Check that the system was implemented in accordance with the approved design; some modifications might need to be re-permitted before inspection.
- To arrange the inspections, get in touch with the utility and AHJ. The homeowner may need to be present, so you’ll need to work with them to arrange that time as well.
During the solar checkup, what takes place?
System quality, equipment compatibility, building code compliance, and whether the system was built as allowed are all assessed during an on-site solar inspection.
During an electrical examination, a licensed electrician must be present in several regions of the nation.
Inspectors frequently inspect the installed system to make sure the roof has the necessary fire pathways listed on the blueprints. This could entail their climbing onto the roof to gauge the separations between modules and roof edges.
An AHJ may occasionally demand that the contractor provide access to the system, which entails setting up a ladder to reach the attic or roof to examine the system and its hookups.
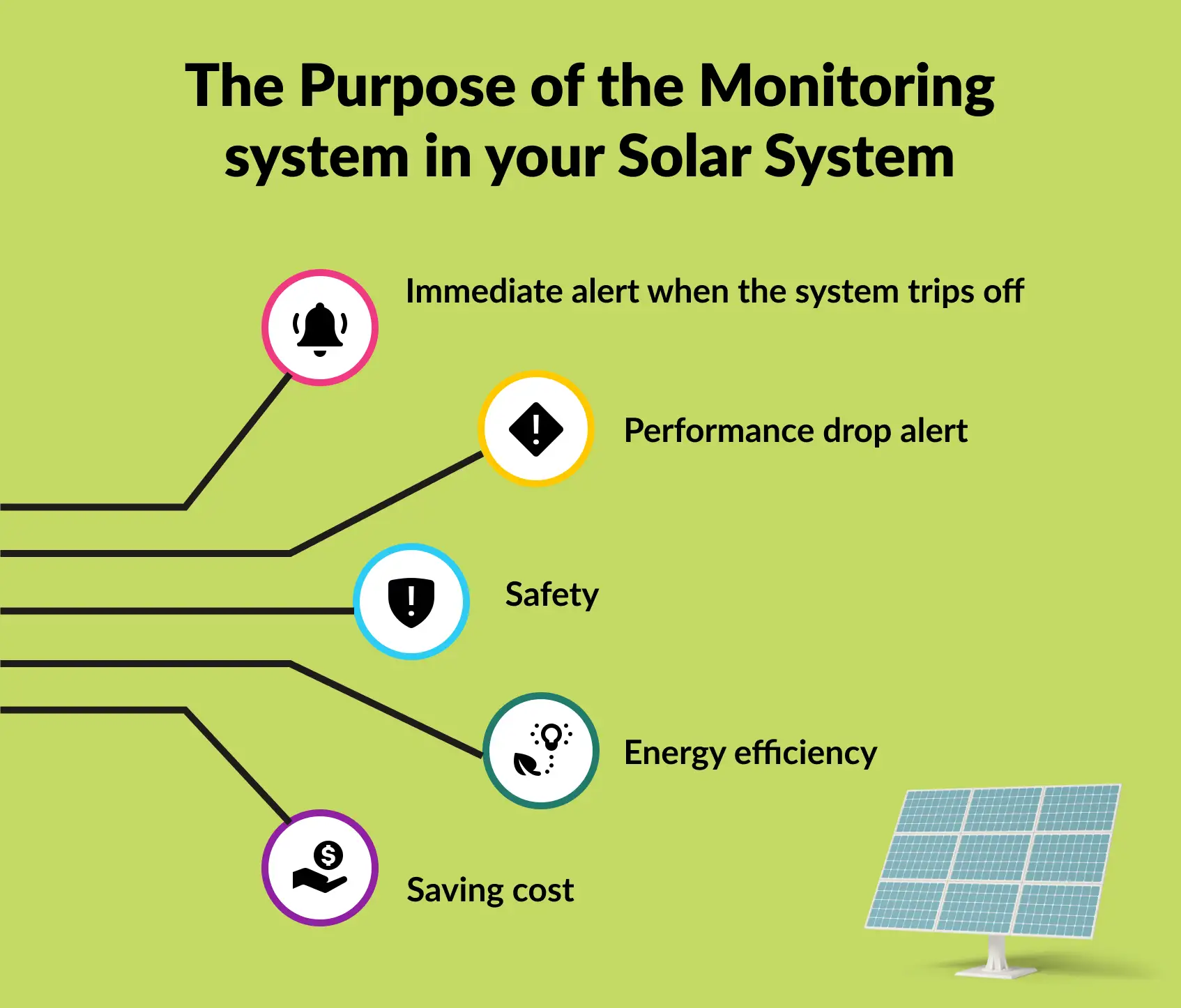
Upon examining the solar panels, a building inspector must confirm that they are installed correctly and in compliance with the manufacturer’s specifications, taking into account the local AHJ regulations, environmental considerations, and the kind of structure.
Solar inspectors check that the system has all the proper sizes and kinds of equipment installed in addition to the panels. This covers the appropriate pipe size and type, wire gauge and type, breaker size, grounding, and more.
Additionally, the inspector will make sure that a functional disconnect mechanism is installed to code in a way that is easily accessible so that in the event of an emergency, the system may be accessed and shut off.
The correct safety labels that identify the system components and functionalities must also be displayed in buildings for them to pass inspection.
The value of solar examinations
Depending on the AHJ and/or utility where the project is installed, an inspection may be required. To make sure the installation conforms with local building rules and connectivity requirements, they aim to make sure it is finished in accordance with the specifics of the approved plan.
Although many utilities have embraced digital or remote inspection techniques to cut down on field delays and serve more consumers, utility inspections are usually a distinct function that must be coordinated with the utility. Clean power can be generated by turning on the system after the utility and AHJ have approved their inspection or inspections.
If an inspection is unsuccessful, the causes may be as simple as labeling a disconnect switch or as complex as going all the way back to the plan-set procedure to make sure the design conforms with AHJ regulations. This entails reentering the system and, in certain situations, making expensive systemic changes.
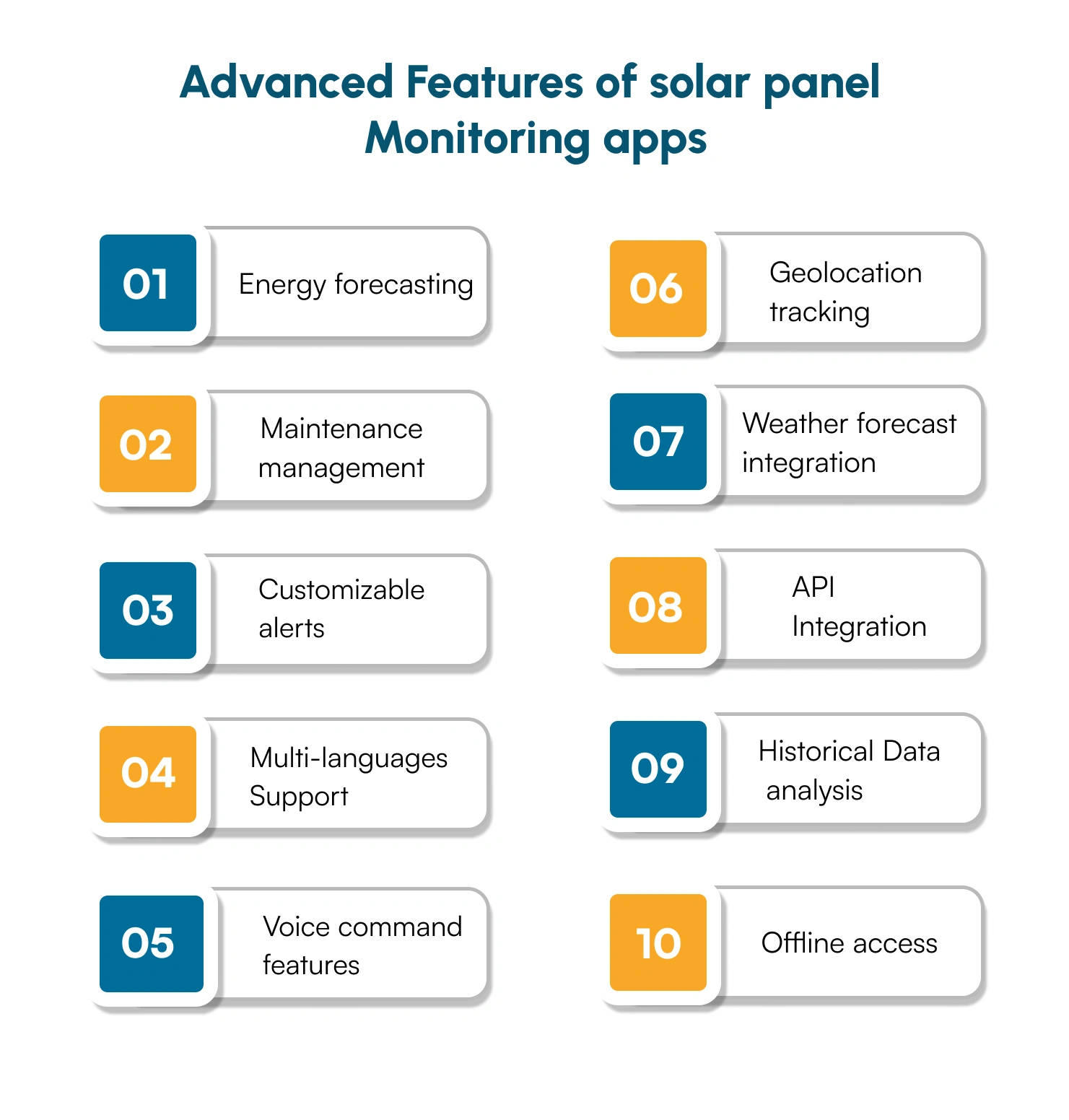
After the system is operational, the homeowner and the installer will typically conduct follow-up checks in case something isn’t working properly.
Now. Let us take an example of several factors that make construction monitoring solutions necessary for large solar energy installations.
Complexity and size: Building a new solar power plant typically entails a number of stages at places that may be kilometers apart. Without physically being on-site or driving from one location to another, construction monitoring systems guarantee that owners and project managers can be informed about everything that is going on.
Quality assurance: Monitoring the construction process helps guarantee that the project aligns with industry standards and design specifications. It’s critical to find issues as soon as possible because delays and rework are costly.
Compliance and safety: Because solar plants use large amounts of electricity, there is an inherent risk to the safety of the workers on the ground. Through the provision of visibility into construction progress and adherence to safety regulations, construction monitoring technologies facilitate compliance.
Cost control: Construction monitoring technologies maximize scheduling, labor productivity, and resource allocation.
Remote Management: Large solar power facilities are frequently constructed in rural and isolated locations. Monitoring technologies improve operational control and minimize truck rolls by enabling remote oversight and centralized management.
Things to think about after the solar examination
As soon as everyone has given their “permission to operate,” or “PTO,” you can ceremoniously “flip the switch” and activate your customer’s renewable energy system.
In order to identify potential problems resulting from damaged or malfunctioning parts, you should now demonstrate to your client how to keep an eye on the operation of their system.
Also read: A complete Guide on Solar Sales- Tips to Improve Solar Sales
Even though inspection approval marks the conclusion of your installation schedule, maintaining contact with your clients is a terrific method to get good feedback and possibly even win new business from referrals.
Streamline the timely solar inspections with the field tracking solution
Here, we are going to list out the essential challenges faced by the companies for solar inspection with the respective solutions. You can get an idea of how field tracking solutions provide essential tips and answers for industries when they struggle in solar inspections.
Challenge #1: Monitoring the progress of solar projects in real time
Delays in identifying issues and schedule deviation result from the lack of an independent platform for accessing and comparing EPC progress as well as from restricted insight into construction. Project managers find it unable to conduct routine monitoring due to large site areas, which leaves them unaware of installation quality and ongoing activity.
? Solution: Physical visits are replaced by periodic flyover assessments. It is possible to compare the number of installed components with the total number of planned components on the site. Sharing immersive insights with stakeholders is possible with 360-degree photos. Deviations are exposed by uploaded site layouts, allowing for prompt corrections for accurate as-builts.
Challenge #2: Cooperation among stakeholders
In order to report progress on-site, clients used a third-party app. The issue was that bills were being sent without evidence of actual installation unless delivery confirmation was obtained. Also a few businesses that were experiencing difficulties modifying their labor size in accordance with project progress and milestone timelines. It is often known that businesses require a means of improving communication, bridging the gap between the office and on-site workers, and expediting the identification and resolution of issues.
? Solution: An annotation feature in the field monitoring app like Lystloc helps identify problems and facilitate communication with the team on the job site. Direct tagging for problem-solving is used in measurement systems to evaluate the quality of work.
Users receive email notifications when there are problems, giving them easy access to the map’s trouble spots- monitoring of truck offloading guarantees precise component deliveries for payment release.
Use technology to identify problems and communicate them to the team working on-site. As a result, improved features that include annotations and notifications for problem detection and resolution were developed. We hope the procedure will go even more smoothly with the introduction of an offline mobile app that is enabled in Lystloc.
Challenge #3: Documentation of the project
Insurance, dispute settlement, and warranty claims are all hampered by the lack of a mechanism for keeping thorough historical records. Successful communication and information exchange both inside and outside the team were being hindered by the absence of internal reporting.
? Solution: Complete historical documentation is provided by periodic aerial progress evaluations. Internal communication is made easier with the help of PDF reports that describe on-site progress. The ability to create reports at the block level also takes care of block-specific logistics.
Try out Lystloc today and ensure your solar inspections are on time!